The author of this article, maxfiner, graduated from Xi'an University of Electronic Science and Technology with a master's degree in signal and information processing. Maxfiner has worked in the wireless communication department of Huawei Communication Technology Co., Ltd., and has many years of experience in engineering project development. It also has algorithm theory research, simulation verification, and corresponding hardware design implementation capabilities. It has practical experience in all aspects of communication physical layer development and design. .
Another important application related is to estimate the delay of the signal. This delay can be the delay on the analog circuit channel, such as measuring the delay of the transmitter RF link. It can also be a delay in wireless space transmission, such as radiation source location in the field of radio monitoring, delay estimation of satellite navigation signals, and so on. This section is devoted to the estimation and application of delays on analog channels. Before introducing specific applications, briefly introduce some background knowledge of mobile communication base station transmitters. There are two purposes for introducing this background knowledge: first, to make a systematic preparation for the relevant delay estimation. Second, the ribbon shows the purpose and power of digital signal processing.
Generally speaking, the physical layer of the mobile communication base station transmitting link can be divided into three parts: a digital baseband, a digital intermediate frequency, and an analog radio frequency. With the widespread application of the zero-IF transmitter architecture, the traditional IF does not exist. The quadrature modulator can modulate the baseband signal to a specified RF frequency at a time. However, after the transmitter's baseband signal is formed, it usually needs to be done in the digital domain before outputting to the DA converter. These tasks include upsampling, clipping (CFR), digital predistortion (DPD), and quadrature modulation compensation. Power control and more.
What are these measures used for? Fundamentally, these measures are designed to overcome the irrational nature of RF analog channels. In practice, these tasks are indispensable, and they directly affect the transmitter's key indicators such as the quality of the transmitted signal, the power of the transmitter, and the power consumption of the transmitter. In theory, these tasks can also be done, but the fierce competition among communication equipment vendors has forced them to do so, and the measures and means adopted in these areas have become the embodiment of the core competitiveness of communication equipment vendors. Effectively suppress each other and show off their powerful weapons.
A brief description is as follows:
The first example: as the peak-to-average ratio of multi-carrier signals and OFDM signals is usually larger, this leads to a larger power amplifier's retreat, and the power amplifier efficiency will be much lower, which is quite uneconomical, so in order to better play Power amplifier advantages require clipping to reduce the peak-to-average ratio.
The second example: a large part of the power consumption of the communication base station is caused by the power amplifier. The efficiency of the power amplifier directly affects the power consumption cost of the mobile operator. Everyone wants the power consumed by the amplifier to be converted into electromagnetic waves as much as possible, instead of becoming pure heat. In order to improve the efficiency of the power amplifier, the digital pre-distortion processing (DPD) is generally required to ensure that the signal does not undergo large distortion when a certain degree of saturation occurs.
The third example: the quadrature modulator on the transmit link generally has a certain degree of gain imbalance and phase imbalance, DC offset, etc. for the input IQ two-way signal, which will result in the output signal after quadrature modulation. There is a local oscillator leakage and image signal generation. This is a problem that analog devices are difficult to completely avoid. In order to overcome these undesirable characteristics, it is generally required to perform quadrature modulation compensation processing. This is often referred to as IQ imbalance correction.
The fourth example: the transmission power of the mobile communication base station transmitter changes with temperature and frequency fluctuations. The power variation due to temperature and the like can reach several dB, which directly leads to a change in the coverage size of the base station. Therefore, the monitoring, statistics and adjustment of the transmission power must be performed in real time.
The above mentioned, whether it is clipping, digital pre-distortion, IQ correction of analog channels, this is a good place for digital signal processing in the application practice. It can be seen that analog devices are difficult to achieve the level of precision we expect. However, we can use digital signal processing methods to compensate for these errors, not ideal characteristics, and compensate, compensate or offset them. It is also a charm of digital signal processing.
Digital predistortion DPD and IQ corrections are usually done using a feedback mechanism. In the specific implementation, a small part of the transmitted signal is obtained through the coupler at the output end of the power amplifier (usually several db smaller than the transmitted signal), amplified by a feedback channel, mixed and AD sampled, and returned to the digital domain ( For example, FPGA), this feedback signal contains the distortion information of the transmitting link (strictly speaking, it also contains the distortion information of the feedback link, but it is generally considered that the distortion of the feedback link is negligible relative to the distortion of the transmitting link) . Based on the preset distortion model of the analog device, the DPD or IQ correction parameters are solved based on the feedback signal and the transmission signal, thereby completing the DPD or QMC correction processing. The purpose of these corrections is to effectively address the undesirable characteristics of analog devices such as power amplifiers or quadrature modulators.
The following figure depicts the entire transmit-feedback mechanism, where the green dashed line indicates the transmit channel and the red dashed line indicates the feedback channel. Whether it is for the DPD of the power amplifier or the QMC for the quadrature modulator, the premise of the correction is that the correction parameters must be obtained. The estimation of these correction parameters is based on the transmitted signal and the feedback signal, because the transmitted signal can be regarded as ideal. The source signal, and the feedback signal contains distortion information of the transmission link.
It can also be said that we consider a transmission signal as a reference signal, and the feedback signal collected through the feedback channel is regarded as a distortion signal. We pre-construct a distortion model for a non-ideal analog device, from which the distortion parameters can be estimated. The information input to this model is used to make the comparison signal and collect the feedback signal.
So, we collect a segment of the transmitted signal and the feedback signal at the same time. What is the difference? Can the distortion component be seen from the waveform of the feedback signal? In fact, whether it is the distortion of the power amplifier or the distortion of the quadrature modulator, it is reflected in the time domain waveform, which is very subtle and not easy to distinguish, but can be clearly reflected in the frequency domain. In addition to some subtle distortion of the feedback signal waveform, there is a delay in the feedback signal waveform relative to the transmitted signal acquired during the same period. This delay is caused by the transmit link and the feedback link. From the perspective of the signal flow, we can understand that we are collecting the transmitted signal from the in-situ flow, and the feedback signal is that the transmitted signal flows around a large circle.
This delay difference has a significant impact on our correction, because the input of the distortion model requires a one-to-one correspondence between the reference (transmit) signal and the distortion (feedback) signal, or, in terms of time samples, one-to-one correspondence. Or, the requirement is two signals in the same time period, which is the premise of the model to estimate the distortion parameters. The delay error between the reference signal and the distorted signal has a great influence on the correct estimation of the model parameters. For digital signals in the digital domain, the basic unit of error is an integer, which is determined by the period of the sampling clock. Generally, the error is required to be within one sampling clock period.
The delay difference between the transmitted signal and the feedback signal can be estimated by correlation processing. At the same time, the transmission signal and the feedback signal of a length are collected, and the correlation calculation is performed. By the peak value of the correlation function, the delay of the feedback signal relative to the transmission signal can be estimated.
As can be seen from the above description, the delay of the signal in the transmission channel can be estimated by correlation calculation, which is a prerequisite for performing digital pre-distortion, IQ imbalance correction and the like.
The next issue - proficient in signal processing design small TIps (10): in the application of radio direction finding, please pay attention!
Disclaimer: Electronic enthusiast network copyright, declined to reprint!
Proficient in Signal Processing Design Small TIps(1): Signals and Information
Proficient in Signal Processing Design Small TIps(2): The Role of Mathematics
Proficient in signal processing design, small TIps (3): the three cornerstones that must be mastered
Proficient in Signal Processing Design Small Tips(4): Several Signals Used Most Frequently
Proficient in Signal Processing Design Small Tips(5): Three widely used mathematical concepts
Proficient in signal processing design Tips (6): How is convolution obtained?
Proficient in Signal Processing Design Small Tips(7): Extremely Widely Applied
Proficient in Signal Processing Design Small Tips(8): Detecting signals submerged in noise
A Dc Motor is any of a class of rotary electrical machines that converts direct current electrical energy into mechanical energy. The most common types rely on the forces produced by magnetic fields. Nearly all types of DC motors have some internal mechanism, either electromechanical or electronic, to periodically change the direction of current flow in part of the motor.
DC motors were the first type widely used, since they could be powered from existing direct-current lighting power distribution systems. A DC motor's speed can be controlled over a wide range, using either a variable supply voltage or by changing the strength of current in its field windings. Small DC motors are used in tools, toys, and appliances. The universal motor can operate on direct current but is a lightweight motor used for portable power tools and appliances. Larger DC motors are used in propulsion of electric vehicles, elevator and hoists, or in drives for steel rolling mills.
Dc motor areas of application: smart home field, robotics, precision medical equipment industry, automotive drive field, electronic products and personal care equipment
Application of the product:
Features: high torque, low noise, small volume, light weight, easy to use, running constant speed, etc., can also be matched with various gearboxes to change the output speed and torque.
Features: small volume, fast speed, stable performance, low price, good speed regulation.
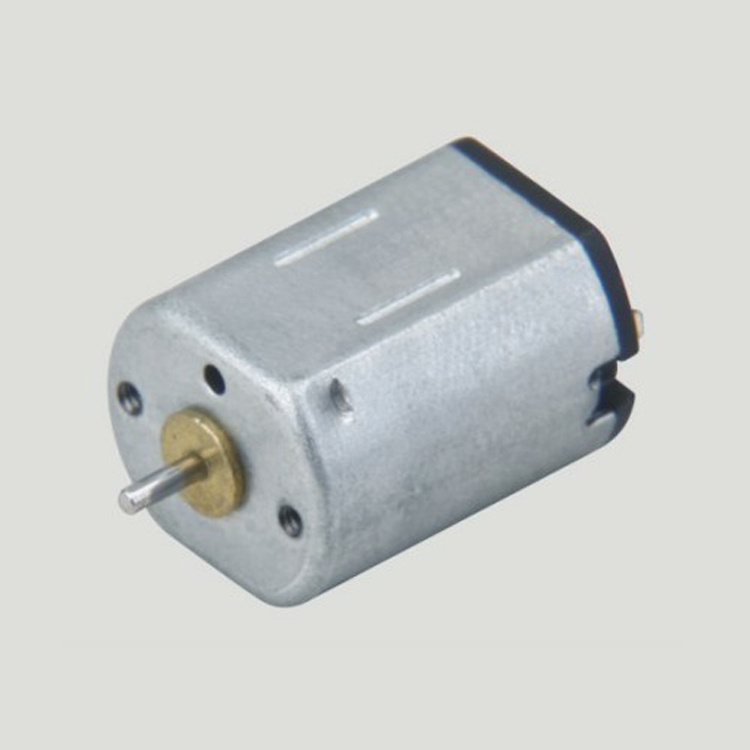
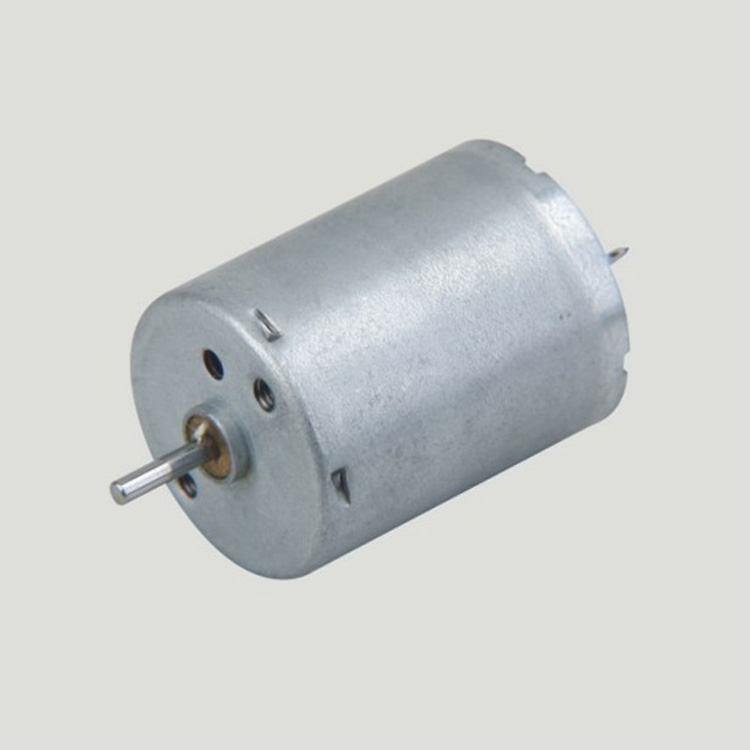
Method of use: the best stable in horizontal plane, installed on the dc motor output shaft parts, cannot use a hammer to knock, knock prone to press into the dc motor drive, may cause damage to internal components, and cannot be used in the case of blocked.
Operating temperature range:
DC motor should be used at a temperature of -10~60℃.
The figures stated in the catalog specifications are based on use at ordinary room temperature catalog specifications re based on use at ordinary room temperature (approximately20~25℃.
If a geared motor is used outside the prescribed temperature range,the grease on the gearhead area will become unable to function normally and the motor will become unable to start.Depending on the temperature conditions ,it may be possible to deal with them by changing the grease of the motor's parts.Please feel free to consult with us about this.
Storage temperature range:
DC motor should be stored ta a temperature of -15~65℃.
In case of storage outside this range,the grease on the gearhead area will become unable to function normally and the motor will become unable to start.
Service life:
The longevity of DC motor is greatly affected by the load conditions , the mode of operation,the environment of use ,etc.Therefore,it is necessary to check the conditions under which the product will actually be used .The following conditions will have a negative effect on longevity.Please consult with us should any of them apply.â—Use with a load that exceeds the rated torque
â—Frequent starting
â—Momentary reversals of turning direction
â—Impact loads
â—Long-term continuous operation
â—Forced turning using the output shaft
â—Use in which the permitted overhang load or the permitted thrust load is exceeded
â—A pulse drive ,e.g.,a short break,counter electromotive force,PWM control
â—Use of a voltage that is nonstandard as regards the rated voltage
â—Use outside the prescribed temperature or relative-humidity range,or in a special environment.
â—Please consult with us about these or any other conditions of use that may apply,so that we can be sure that you select the most appropriate model.
when it come to volume production,we're a major player as well .each month,we rurn out 600000 units,all of which are compliant with the rohs directive.Have any questions or special needed, please contact us, we have the engineer group and best sales department to service to you Looking forward to your inquiry. Welcome to our factory.
Dc Motor
Dc Motor,Small Dc Motor,Mini Dc Motor,Robot Dc Motor,Dc Motor With Gearbox
Shenzhen Shunchang Motor Co., LTD. , https://www.scgearmotor.com