ADI provides developers with solutions for large commercial aircraft with proven experience in optimizing system-level signal processing performance and a wide range of products. The ADI solution provides a range of products related to this application, such as those used in aircraft navigation subsystems, communication subsystems, radar and monitoring subsystems, power and propulsion subsystems, and cabin entertainment subsystems.
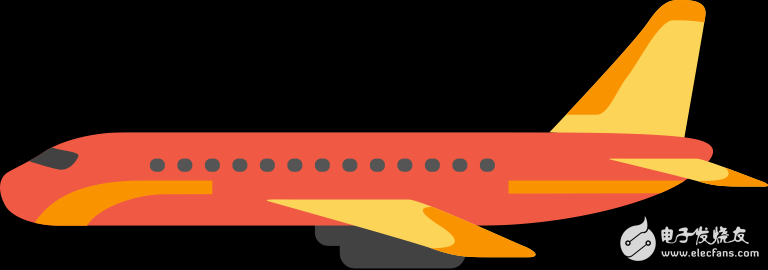
ADI focuses on the support of commercial aviation
ADI has a team of marketing and application design members dedicated to supporting the aviation industry. The current focus is on the following five areas:
01
Avionics - Attitude Reference System
MEMS Inertial Measurement Unit (IMU)
Interface driver and isolator
High speed data converter for analog input
02
Avionics - Communication
Transceiver solution
Air to ground
Air-to-air
Amplifiers, filters, isolators and modules
Low-power wireless monitoring
03
Power and propulsion
High temperature / enhanced performance
Power management and monitoring
Drive and control
04
Safety and monitoring
radar
Surveillance and weather
Obstacle detection
HUMS
Accelerometers, converters and DSPs
ADS-B/Wireless Monitoring
05
body
Motor Control Circuit / Power / Isolation
Encrypted and trusted networks
LVDT/RVDT
Precision converter
Linear amplifier
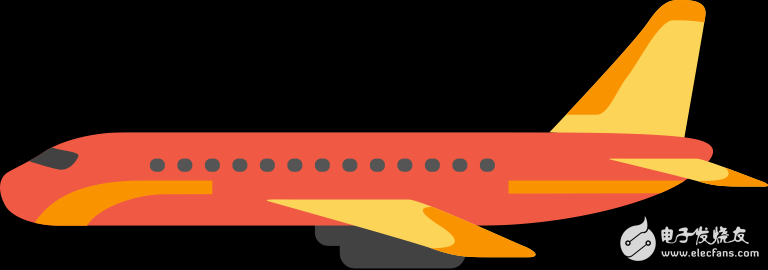
Why choose ADI
ADI has a team dedicated to supporting aviation development and production in a wide range of markets around the world, and continues to expand the applicability of its products to support fast-growing markets. Also, ADI has expertise in building and supporting customers' avionics and unmanned systems markets.
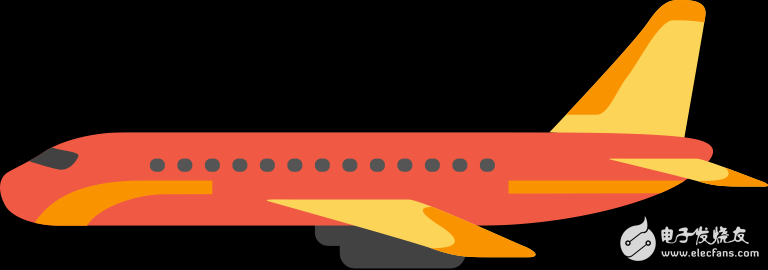
Key challenges and system design considerations
The main challenge in aerospace design is -
RTCA ( Aeronautical Radio Technical Committee ) considerations and DO 178B/C, DO 160 and DO 254 functional safety certification requirements. These requirements are extremely rigorous and detailed, requiring careful consideration of the design and the components it contains.
Many problems revolve around complex components, redundant paths, and known failure modes. Certification requirements are becoming more complex based on the impact on flight safety.
The aviation industry is using electronic systems to replace pneumatic and hydraulic components. In terms of temperature, corrosivity, etc., components and components are subjected to harsher environmental conditions.
ADI supports many major aerospace customers and provides the documentation required for DO 178/DO 254 certification. Equally important, ADI has high-performance device processes and catalogs for the aerospace industry that use nickel-palladium-gold leadframes (to reduce tin whisker effects) and special non-copper internal wire bonds (corrosion-resistant) for operating temperature ranges. It is –55°C to +125°C (partially up to +175°C).
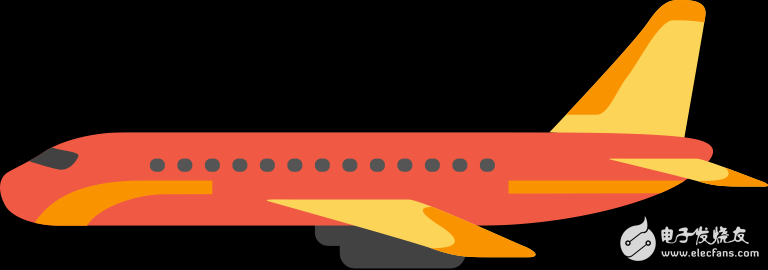
Commercial aviation signal chain
![]() |
![]() |
![]() |
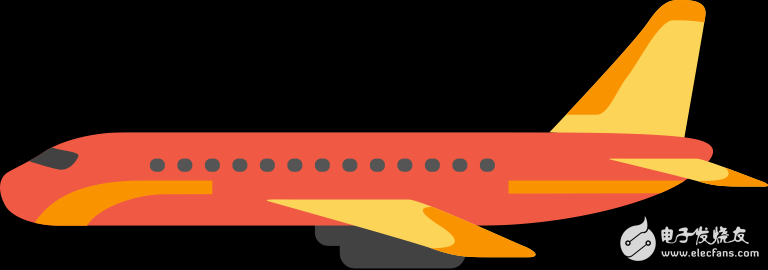
Enhanced product
Currently, there are more than 100 enhanced product (EP) products and more than 600 devices using nickel-palladium-gold lead structures in the ADI catalog . Analog Devices continues to introduce new EP devices to support the commercial aviation market. In the future, ADI will continue to transform traditional devices into practical EP devices.
The product is rated for temperatures from –55 to +125 °C;
Pin surface treatment defaults to NiPdAu, and some packages use SnPb;
EP devices will have separate data sheets;
The strictly controlled production facilities include an assembly plant, a test plant and a manufacturing plant.
Casting is the process of pouring molten metal into a mold and cooling and solidifying to obtain parts with the desired shape and properties. Casting is a commonly used manufacturing method, with low manufacturing cost and great process flexibility, and can obtain complex shapes and large castings. 50 to 60%.
Due to the increasing requirements for casting quality, casting accuracy, casting cost and casting automation, casting technology is developing in the direction of precision, large-scale, high-quality, automation and cleaning. Casting technology, special casting technology, casting automation and casting simulation technology have developed rapidly.
Casting Parts,Stainless Steel Casting,Investment Casting Meat Mincer,Ductile Iron Sand Casting Parts
Tianhui Machine Co.,Ltd , https://www.thcastings.com