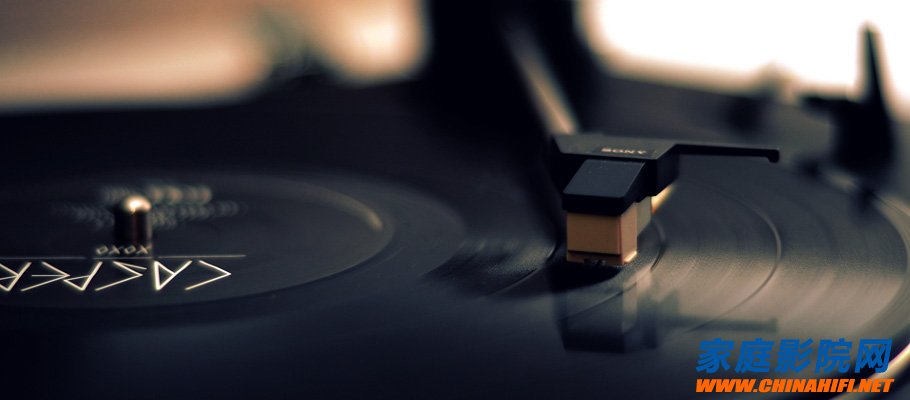
The process of recording a vinyl record from recording to distribution is very complicated. From the practical point of view, we start directly from the marking of the record, and through the understanding of the process of marking to the tableting process, we will establish an orderly adjustment of our later turntable system. basis.
The master of the record is recorded by a sharp knife, which is a typical mechanical recording. When the master of the early record was burned, the musicians played or sang against the big horn, so that the sound was sent into the cylinder, passed to the diaphragm at the bottom of the cylinder, and driven by a metal film driven by the sound energy. As the amplitude of the sound wave changes, the intensity of the sound wave changes the curved groove on the rotating wax disk. This process of converting sound energy into mechanical energy is called a recording disk. After the sound signal is recorded on the wax plate, it is also subjected to vacuum coating and electroforming to form a metal mold. It can then be used to suppress the record. Such products are the most primitive stage of the recording process.
Since the emergence of tube amplifiers, the production of records has gradually become electrified, and the driving of the knives has changed from the original mechanical type to the electric (moving-coil) structure, musicians play and sing through high-fidelity microphones (microphones). The sound energy is converted into an audio current that is amplified by the electron tube to drive the knives. The film that can be engraved with precision grooves quickly replaced the wax plate of the past, which made the sound quality of the record significantly improved. At this time, the recording disc is a conversion process from sound energy to electric energy and then to mechanical energy.
The birth of magnetic recording technology changed the flow of the film engraving process. Record the sound source with a tape first, then perform the engraving by tape playback. This engraving process facilitates the editing of music content and the preservation of the program source. Due to the quality of the tape itself, the sound quality of the record is discounted, and the record actually becomes a replica of the tape. With the development and improvement of magnetic recording technology, the sound quality of recordings is rising.
In the 1980s, modern record engraving equipment was technically advanced. The main technical indicators such as frequency characteristics, signal-to-noise ratio, distortion, dynamic range and squelch have reached extremely high levels. In order to make full use of these advantages of the record, some fever record manufacturers have returned to the development and production of direct-recorded records. Directly recorded records are marked with text, such as DIRECT TO DISC, DIRECT DISC RECORDING, and DIRECT METAL MASTERING (abbreviated as DMM, see Figure - it is a special sign for TELDEC direct recording). No matter how the words are grouped, they all have the same meaning, that is, "direct engraving records" is simply referred to as "direct recordings." The process of directly recording a record is a process of converting from acoustic energy to electrical energy to mechanical energy. It does not have the procedure of recording, mixing, and reproducing the tape. The conversion process is the most direct and simple, and the sound quality is also the best. Since there is no master tape, the number of discs that are suppressed is very limited. Therefore, the words "LIMITED EDITION" are limited on the record. (The limited issue is not artificial. The number of direct masters is limited. Once the master is scrapped, the master will be scrapped. Out of print), there is also a direct labeling COLLECTORS EDITION "Collection Edition". The most representative ones are the SHEFFIELD LAB (Sherfield Labs, commonly known as the trumpet flower company) in the United States, and the TELDEC company formed by the combination of DECCA and TELEFUNKEN in the United Kingdom. They are all advocates of direct recordings. The sound quality of direct-recorded recordings is very good, but the production process requirements are very high. Generally, record companies do not dare to easily touch the fingers. Therefore, there are only a handful of record manufacturers with straight-cut craftsmanship. The trumpet record company is a typical representative of direct-recorded records. There are not many records in his family, but Zhang Zhang is the best. Many records are out of print. It is quite difficult to collect them today. Many of the TELDEC release albums are produced in direct DMM mode, and the sound quality is quite impressive. It’s true that there are so many high-fidelity brand-name albums.
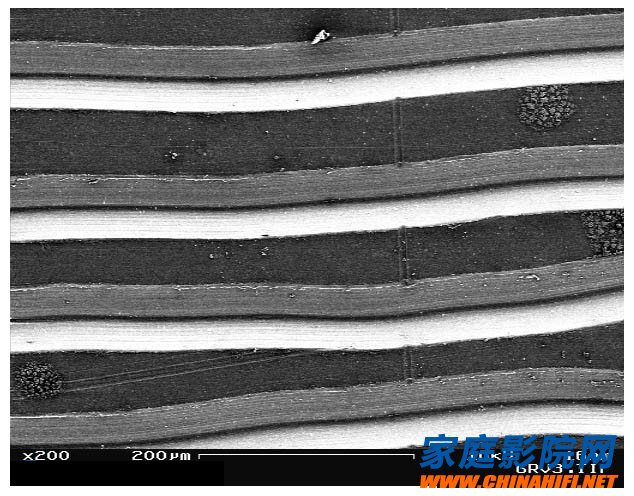
(The sound groove of the vinyl record, scanning electron microscope shooting 200 times magnification, it can be seen that a small horizontal scratch is not a serious problem, dust on both sides of the sound groove is a scourge)
There are two kinds of record pressing processes: one is the embossing method, which softens and softens the pressed plastic sheet and sends it to the template for pressure setting. This pressing process is mostly used for the production of film discs, which are indeed very thin and have a sheet thickness of only 0.15-0.5 mm. Because the film base is thin and soft, the quality of the recorded signal is not high, and it is mostly used for voice and some popular songs that are not demanding, and the price is very cheap. In the high fidelity era, today's film records have long disappeared. The second is the embossing method, in which the hot-melt vinyl is injected into the mother cavity and then subjected to pressure setting, which is a standard process for compact recording. It's very simple to say. In fact, the process of suppressing the recording is very complicated. This is not the scope we need to understand.
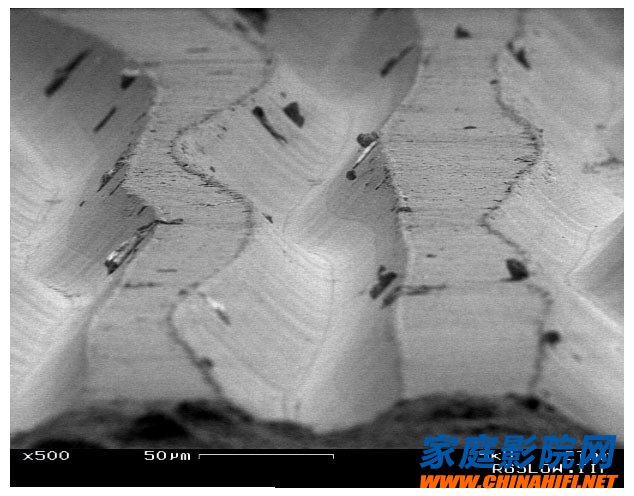
(the sound groove of the vinyl record, scanning electron microscope shooting 500 times magnification)
Next, let's take a step further and learn about the sings of the record. The sing is also called the sound groove or sound groove. The sound groove is the smallest unit that constitutes the record, and the audio signal is recorded on this minimum unit. Let's take a look at the process of burning the record master: as the turntable rotates, the knives heated to a specific temperature vibrate on the surface of the master film driven by the coil signal current, and begin to sculpt the film (ie, scribe) Longitudinal engraving is the initial engraving system, and horizontal engraving is the only engraving system for mono recording. Since the tip end section of the knives is approximately triangular, the engraved sound grooves are uneven and uneven regardless of the longitudinal or lateral system. The cross section of the sound groove is V-shaped. To avoid crosstalk, the spacing between adjacent slots should not be too narrow. The number of sound grooves recorded per centimeter of the Y axis of the surface of the record is referred to as the sound slot density. In the 78-turn era, the material and processing level of the stylus are very low, the needle tip is relatively thick, the recording accuracy is not high, the sound groove has a wide V-shaped mouth, and the sound groove density is very low, so it is called a coarse-grain record ( Coarsegroove record), the 78-revolution record has already withdrawn from the market due to noise, distortion, and short singing time. The angle of the V-shaped cross section of the sound groove is called 'including angle', usually 90°. The width and depth of the groove depend not only on the depth of the entrance when burning, but also on the change in the sound signal. The sound density of the 33-thirds and 45-turn records is high, and the narrowest sound groove width is only 1/20 mm. Compared with the 78-turn thick grain, we call 33 and 1/3 and 45-turn records as dense. Microgreove record, which has low noise, low distortion, long recording time, low rated needle pressure and low singer loss.
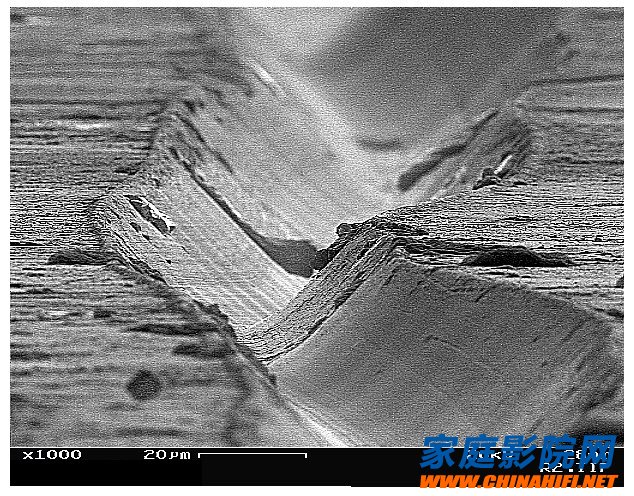
(the sound groove of the vinyl record, scanning electron microscope shooting 500 times magnification)
Stereo replacement mono is the greatest revolution in recording and sound history, and is the beginning of true HI-FI. Stereo recordings record two channels simultaneously in one sound channel. The left channel is recorded on the inner side wall of the sound channel and the right channel is engraved on the outer side wall. The recording direction of each channel is perpendicular to the respective wall surface and maintains a 45° relationship with the center line of the knives. This is the origin of the 45°/45° standard.
The burning sound groove is quite similar to the ploughing of the field. The difference is that the ploughing field is not ploughed, and the recording sound groove is reversed. According to the relative motion principle, there is no difference. The knives and the horizontal surface of the turntable are not at an angle of 90 degrees, but have a certain inclination, which is called a vertical burn angle. The method of definition is to make a connection between the fulcrum of the arbor and the tip of the shank. It is appropriate for this angle. It was not until the late 1970s that the international standard stated that the standard was 20±5°. Since the vertical information content in the sound groove of a stereo record is much larger than the horizontal information, accurately setting the vertical burn angle is of great significance for reducing distortion and ensuring sound quality.
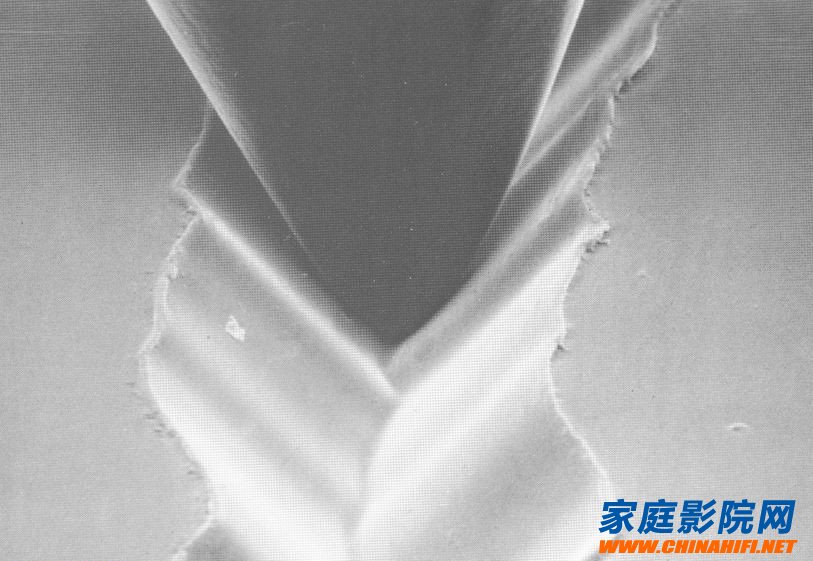
(The stylus tip is in the sound groove of the vinyl record)
The record sound channel is an Archimedes spiral line consisting of four parts from the outside to the inside, in the order of: introduction slot, sound slot, excess slot, lead slot and end slot. The pitch of the lead-in slot is much wider than that of the sound slot, and the length of time that the slot is introduced into the slot is not small. The shortest is only a few seconds. You can't wait to sit down and start singing. When you listen to these records, you must run to the seat. The longest slot is 10 to 15 seconds. You can take it easy after you sing. Returning to the seat, drinking a cup of coffee, and setting a certain god, this is a very scientific and humanized design. The stylus is introduced into the sound groove by the introduction slot, and there are several seconds of silent excessive grooves between the segments, and the excessive groove pitch is also wide, which can be distinguished by the naked eye. The end of the sound groove is connected to the wider groove of the lead groove, and after the music is finished, the stylus is led to the end groove by the lead-out groove. The termination slot is a closed loop design that allows the stylus to stay in place, preventing the stylus from continuing to slide inwardly and damaging the valuable stylus. The poorly finished termination slot 'clicks' is annoying, and the well-designed termination slot is very quiet.
37V Lithium Polymer Battery,Lithium Polymer Battery,3.7 Lithium Polymer Battery,3.7V 4000Mah Lithium Polymer Battery
Langrui Energy (Shenzhen) Co.,Ltd , https://www.langruibattery.com